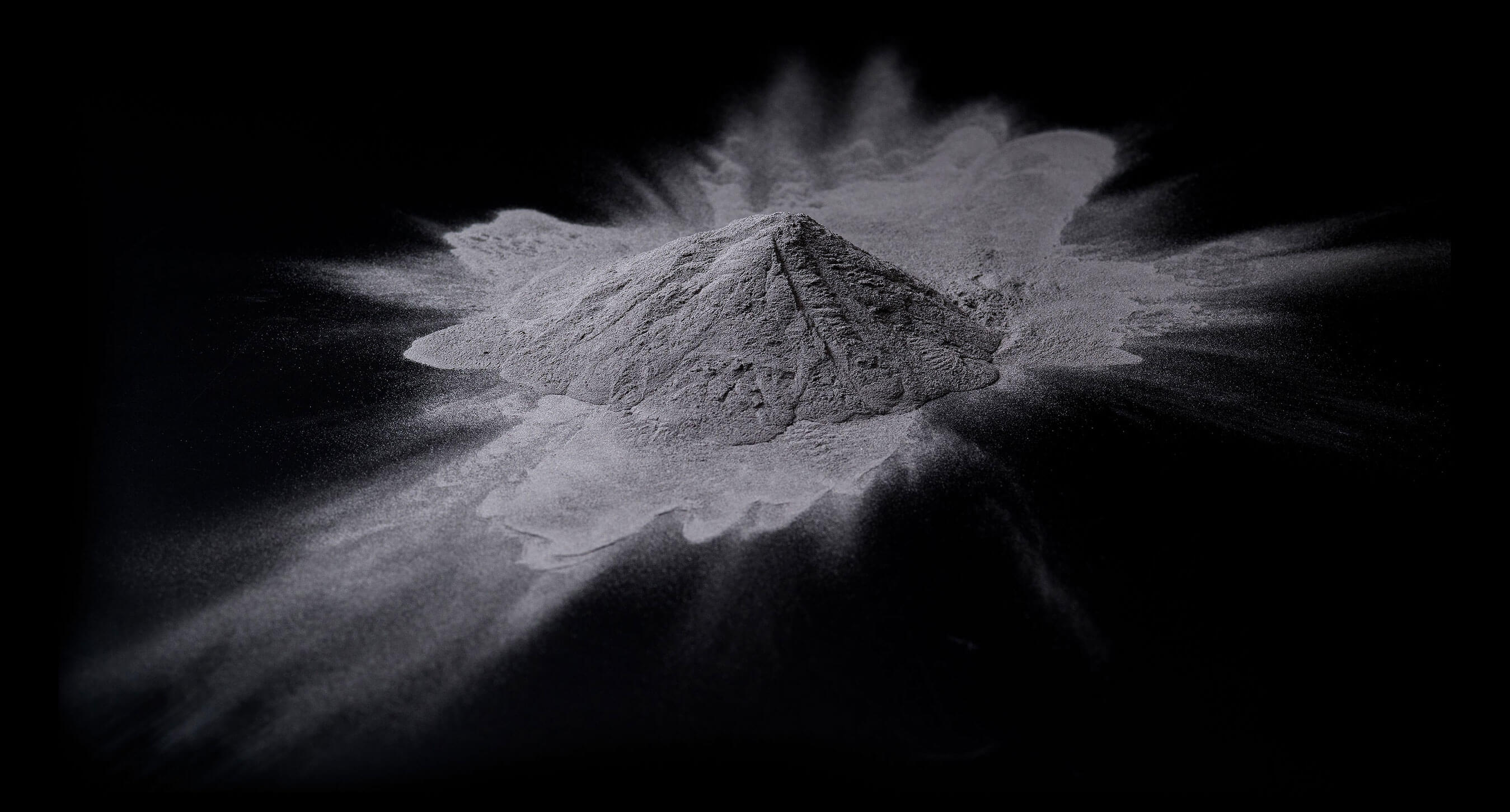
Powder
Advanced metal powders for developing next-generation products
Under the concept of "advanced metal powders for developing next-generation products!", we
develop a wide range of powder materials for various business needs.
Our greatest strength is our ability to stably supply high-quality metal powders that no
other company can imitate, thanks to our proprietary technologies developed in-house.
In particular, our amorphous alloy powders have especially high market demand. In 2004, we
established our proprietary production method called "S.W.A.P.®" by being the first company
in the world to successfully mass produce amorphous alloy powders.
Our company boasts of the world's leading market share in metal powders.
* Distribution of our amorphous powders produced by the atomization method
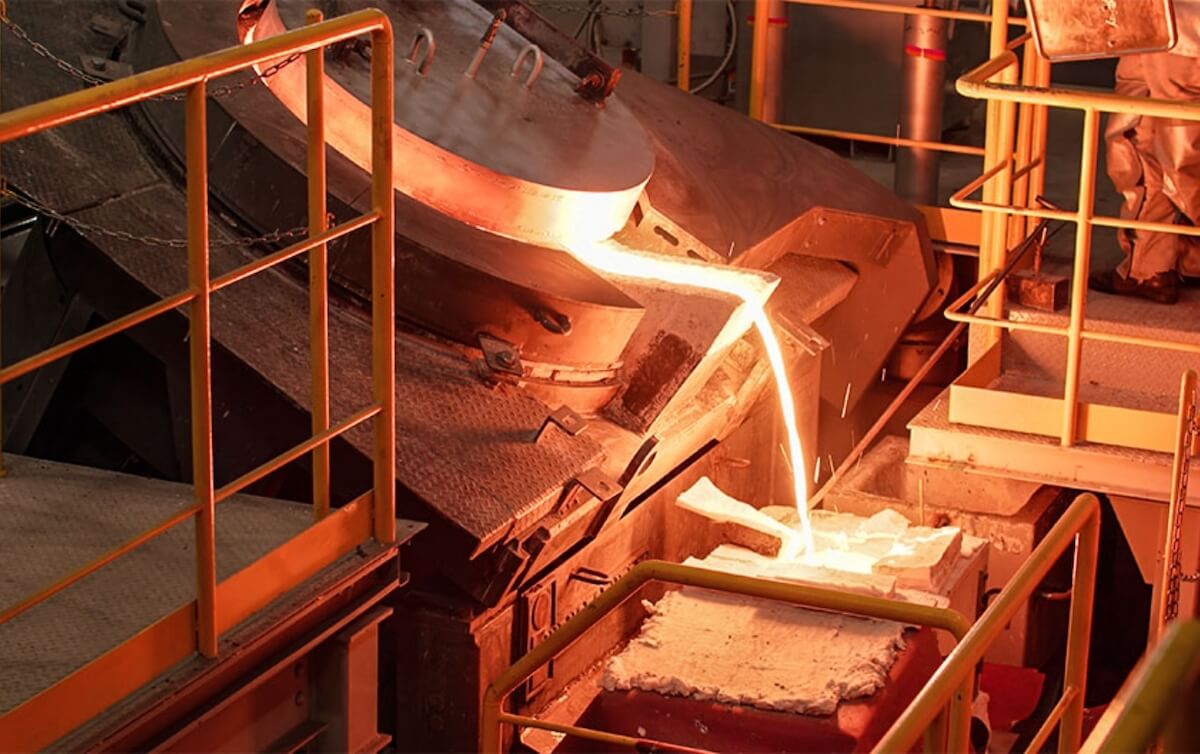
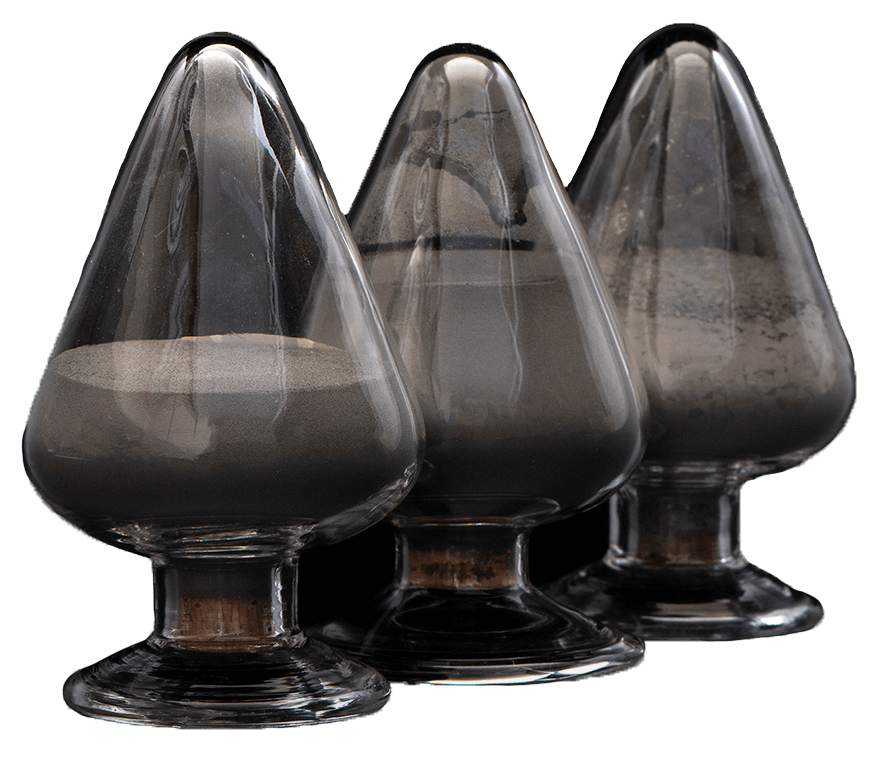
01 Powder manufacturing technologies
in the industry
Distinctive characteristics of our industry-leading superfine metal powders
We utilize the water atomization method, which enables high-yield mass production of superfine powders, and our proprietary S.W.A.P.® method, which was the first in the world to achieve mass production of amorphous powders.
- ● Super-rapid cooling technology
- Enables various alloy designs.
- ● Technology for manufacturing superfine powders
-
We can manufacture finer metal powders.
Accommodates a wide range of customer needs.
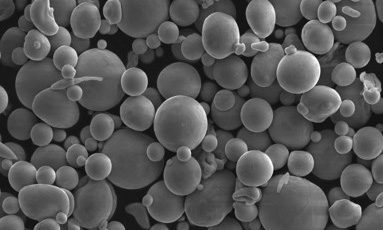
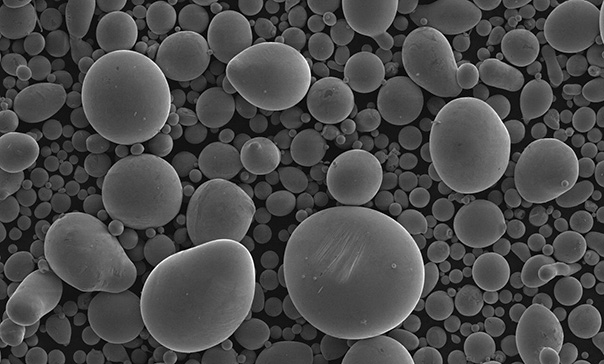
02 Powder processing technologies
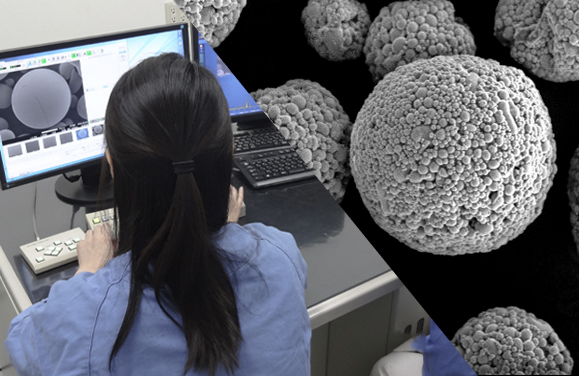
Powder processing technology
Powder processing technologies such as surface modification, granulation, and heat treatment that improve powder properties
03 Products and characteristics
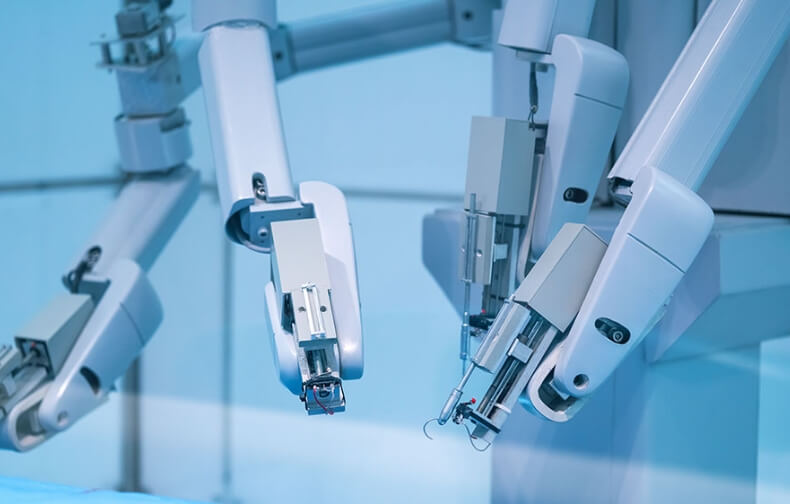
World’s most advanced products
Used in the world's state-of-the-art products including electronics, automotive and medical equipment, and robots
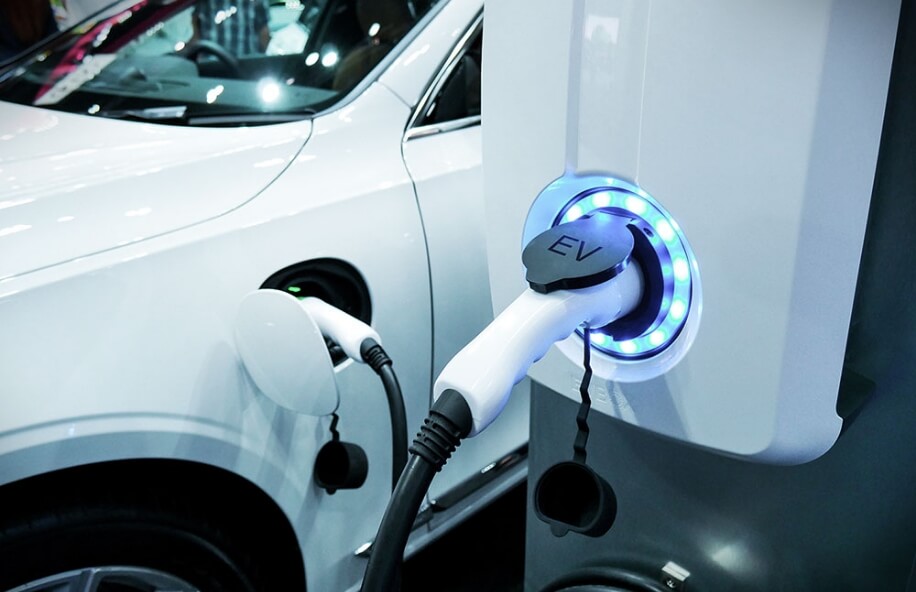
Future products
Raw materials for the electronic parts of futuristic products including 5G and self-driving/electric vehicles
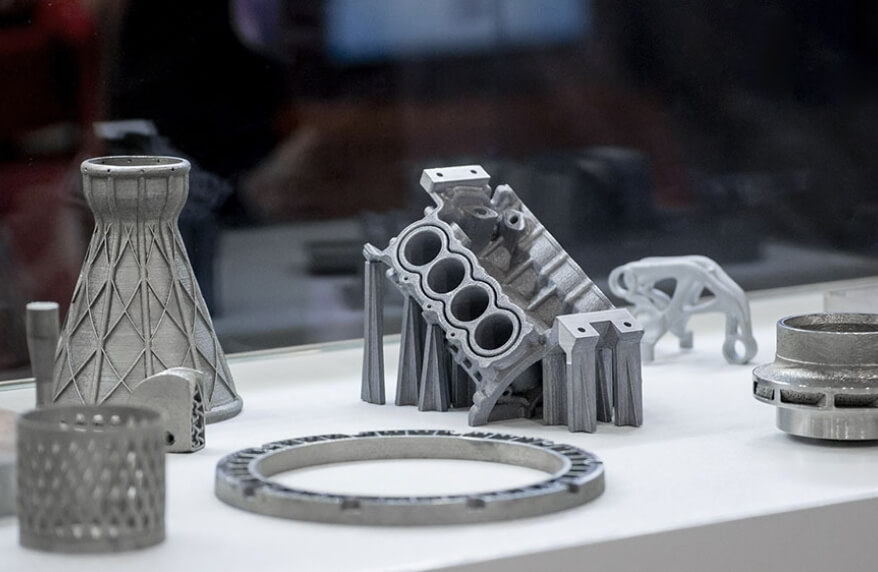
3D modeling raw materials
Raw materials for stereolithography using 3D metal printers
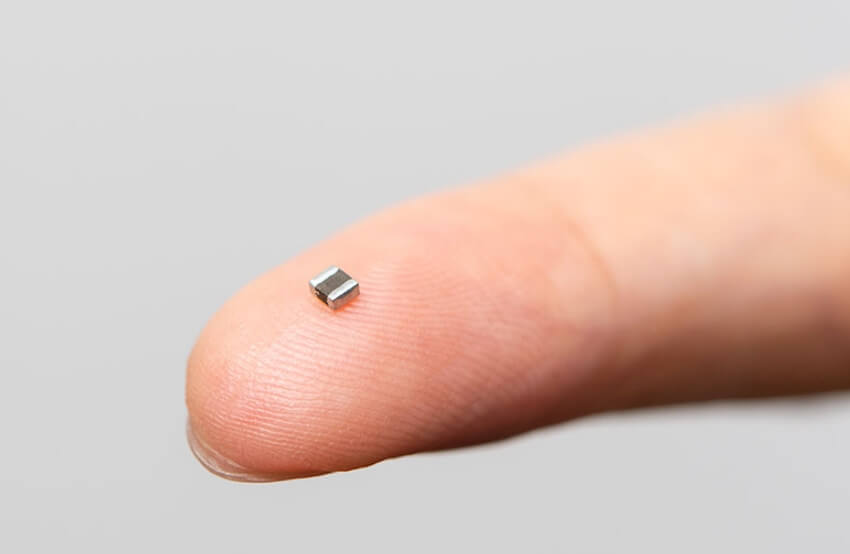
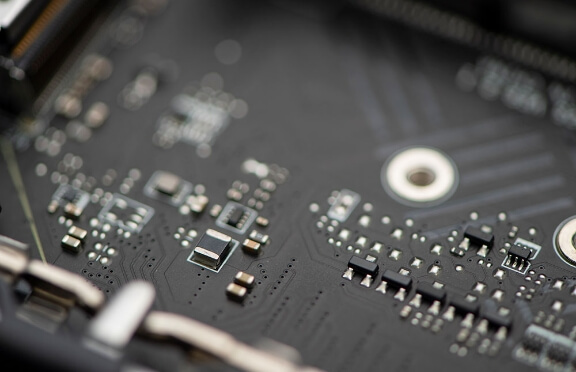
High performance materials
High performance materials that help reduce power consumption and size, and that support high frequencies and large currents
Production and distribution processes
* Distribution of our amorphous powders produced by the atomization method
Purpose | Representative product |
---|---|
Sintering | MIM Powder |
Granulated powder for press-and-sinter | |
AM Powder | |
*Stainless steel, Heat resistance steel (316L, 17-4PH, etc.) | |
Magnetic | Amorphous, Nanocrystalline powder (KUAMET®) |
Super fine powder (ATFINE®) | |
Soft magnetic alloy powder (Fe-Si-Cr, Fe-Ni, etc.) | |
*Enhance performance by Insulation and Anneal system | |
Others | New alloys and experimental lots are available |
Ferrous powder (Low alloy steel, KOVAR, etc.) | |
Non-ferrous metals (Al alloys, Mg alloys, etc.) |
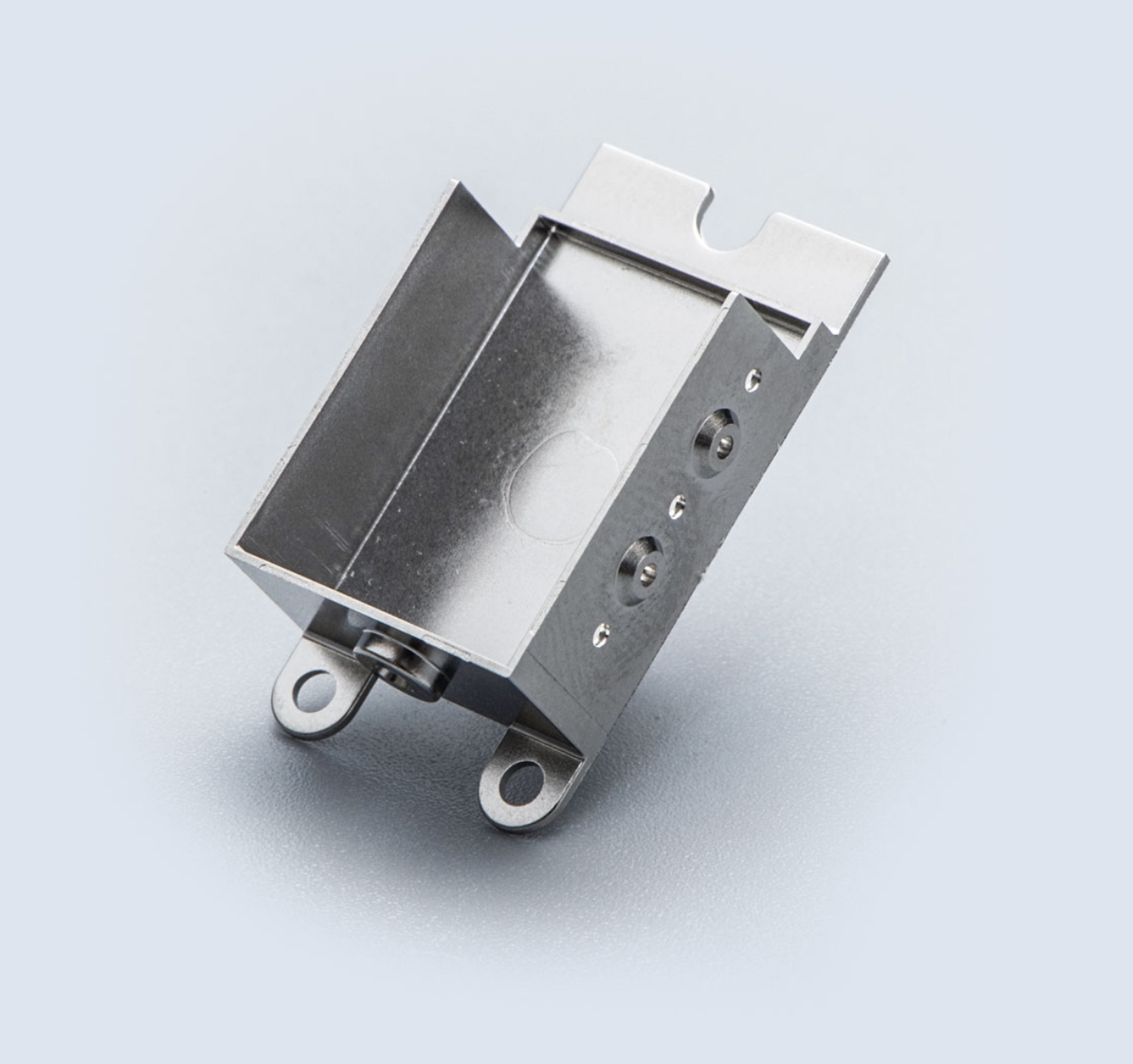
Injection
Molding
metal processing
State-of-the-art metalworking process that combines the characteristics of injection molding and powder metallurgy
MIM is an acronym for metal injection molding, which is a high-precision metalworking method
capable of mass-producing products with complex shapes made from processing-resistant
materials.
We are one of the few metal powder manufacturers in the world the operate a seamless
production system that covers the entire process through to parts processing (MIM).
We are constantly taking on challenges in new areas to produce products that meet our
customers' needs, such as achieving mass production of MIM parts using titanium, which is a
material suitable for medical applications.
01 One stop
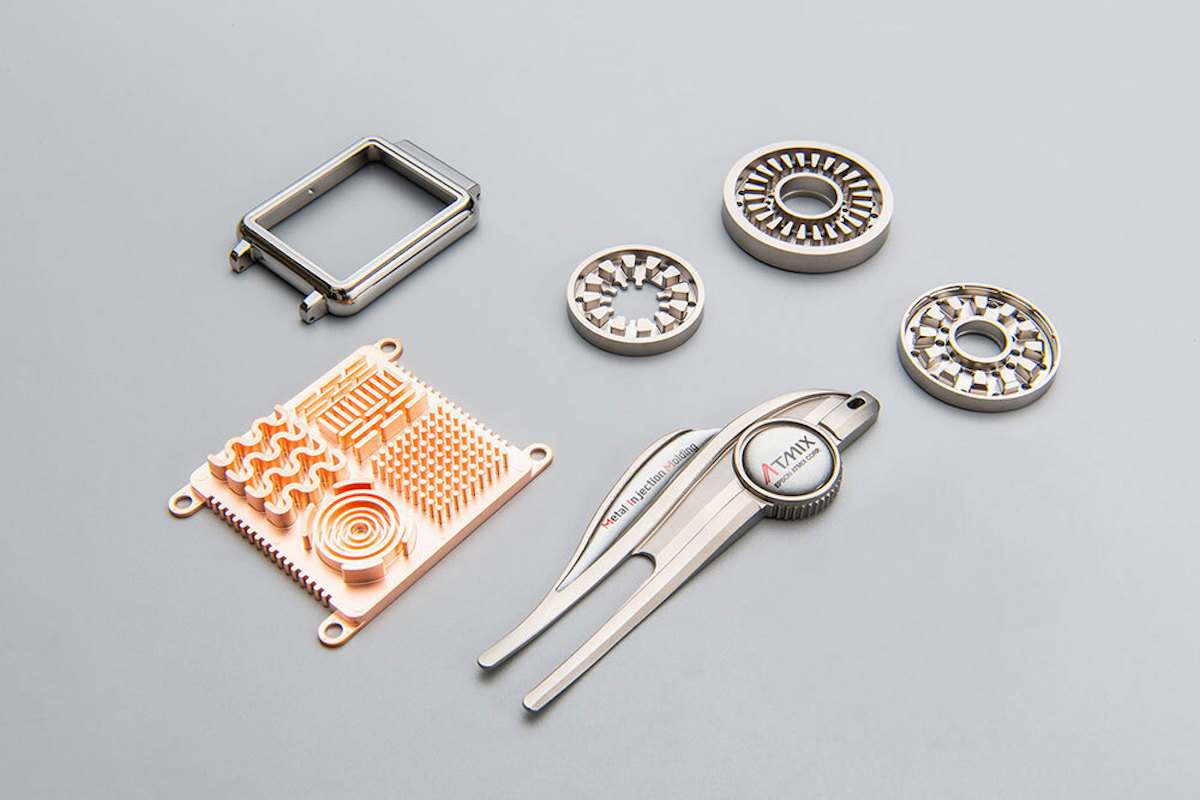
Globally rare business model that seamlessly covers the entire process from metals powder manufacturing to MIM
Our business model that seamlessly covers the entire process from manufacturing metal powders as raw materials through to MIM is without precedent globally. This unique approach enables us to process parts of various types and shapes of steel for diverse property needs while maintaining MIM's characteristics.
One-Stop Flow
02 Technical capabilities
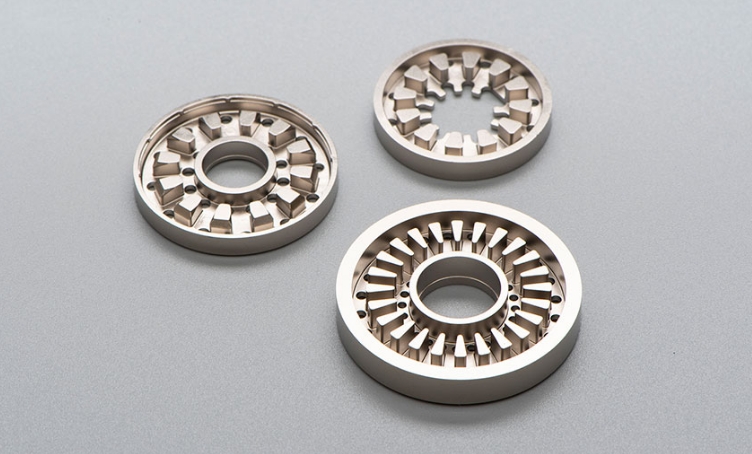
Stereolithography technology
Since we use our own metal powders as raw materials, we can mass produce stereolithography parts that accommodate our customers' needs for strength (density) and properties (thermal conductivity, magnetism, etc.) as well as materials (steel types).
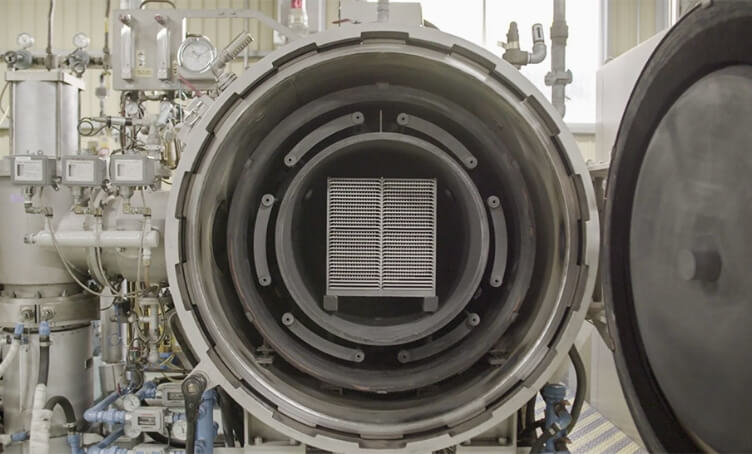
Degreasing and sintering technologies
Using our high quality raw materials and proprietary know-how cultivated over many years, we can handle various process-resistant materials in addition to producing high density stainless steel.
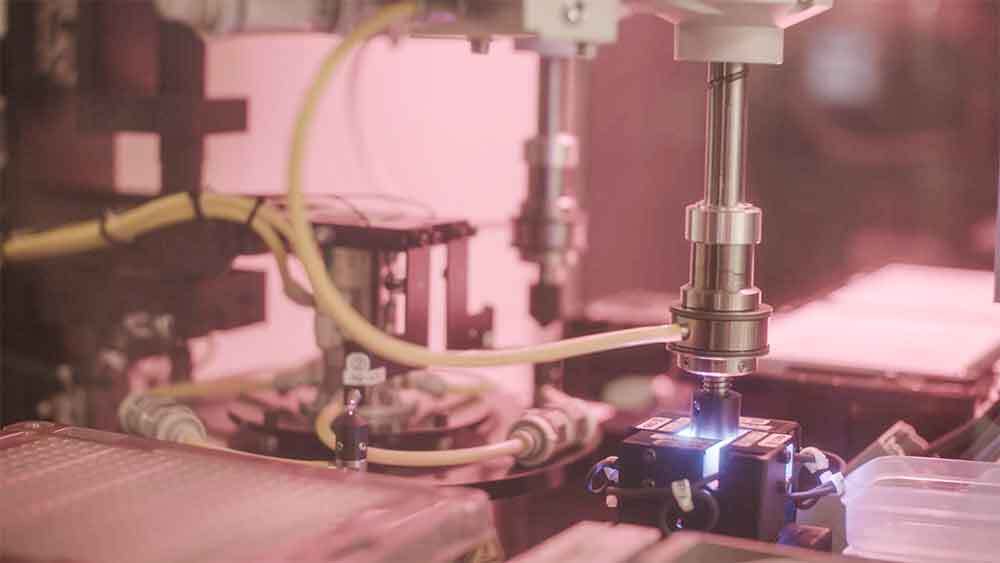
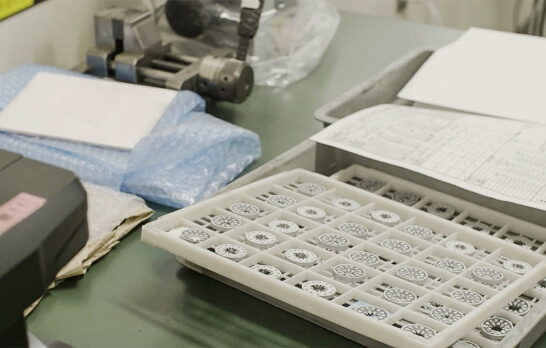
Possess know-how and technology
Know-how and technologies cultivated in advance of other companies
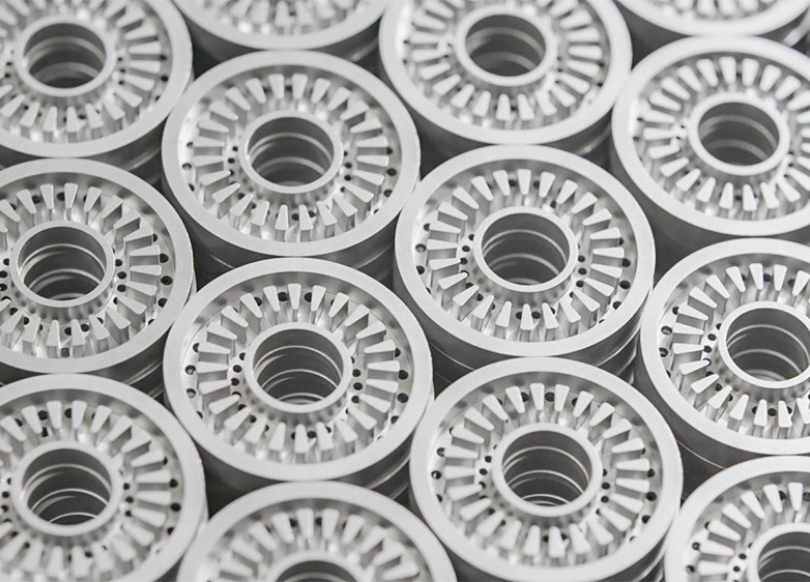
Suitable for mass production of small parts
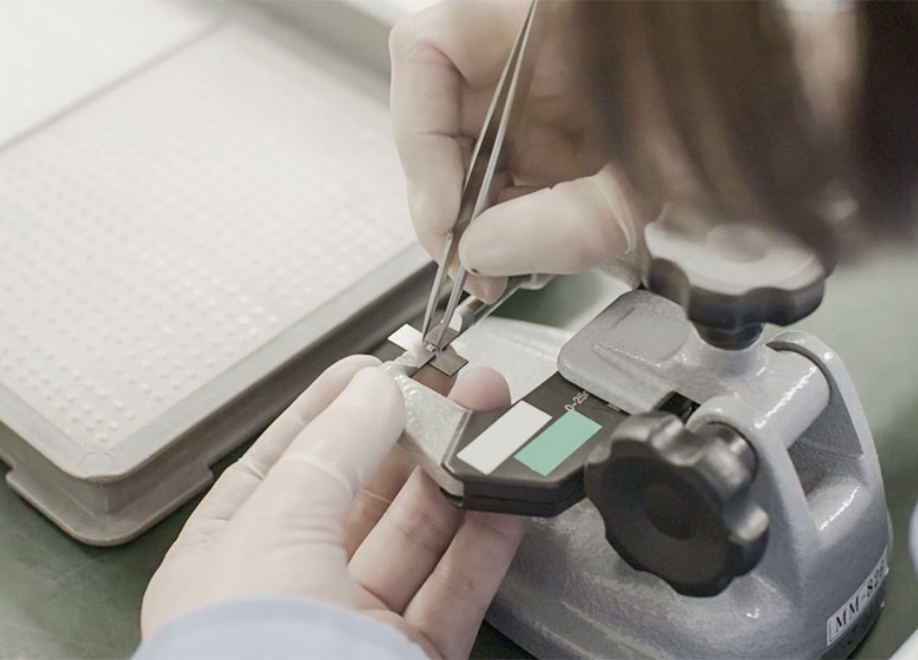
Manufactures various parts
Manufacturing of parts with complex shapes as well as high density and strength
Titanium | We employ our own proprietary technology to control machine strength. |
---|---|
Magnetic alloy | Products are densified, giving them magnetic properties equivalent to those of products made from wrought materials. |
Stainless / Others | Our MIM technology is compatible with all types of steel, including stainless and heat-resistant alloys. |
High quality mirror finished surface MIM |
Through our original powder development/manufacturing and MIM sintering technologies, we
provide MIM materials equivalent to wrought materials. These technologies achieve high quality polished surfaces with high aesthetic appeal. |
Pure copper MIM |
Our proprietary MIM sintering technology controls oxygen content. We have achieved high thermal conductivity equivalent to that of oxygen-free copper. |
Thin wall MIM / Deep carved large MIM |
Thinning of all parts/multi-component integrated shapes are possible. - Save space by downsizing parts. - We can realize difficult shapes by press working and cutting. - Find ways to reduce person-hours and costs by unifying pipes and horizontal hole shapes. |
Product example
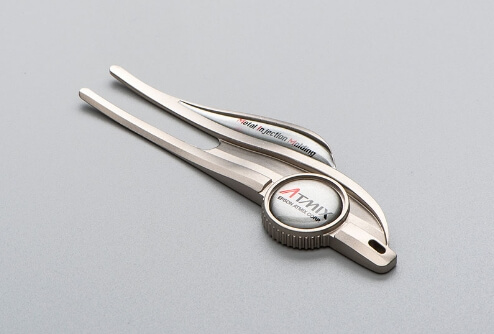
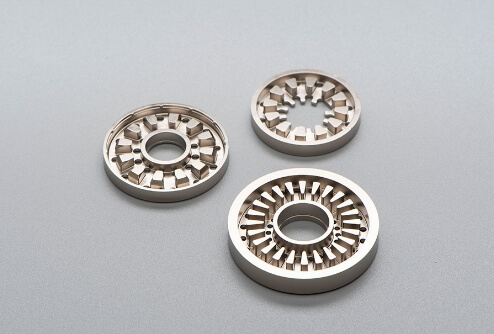
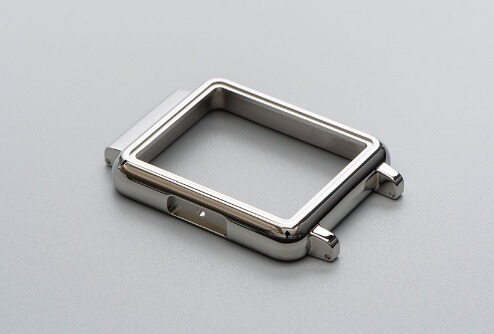
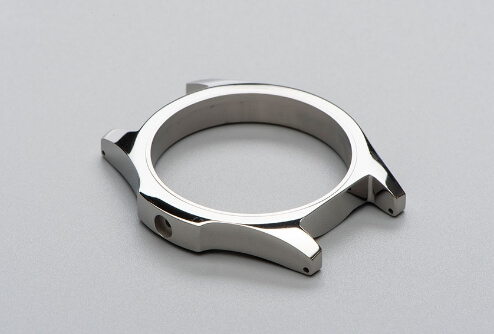
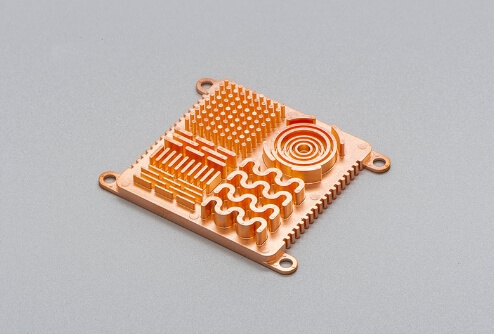
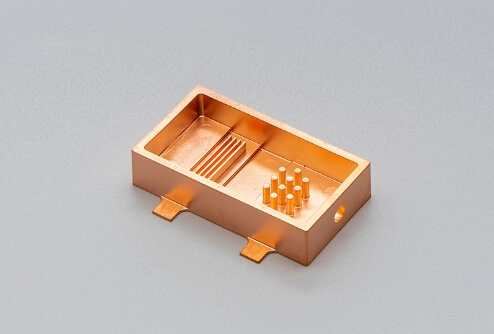
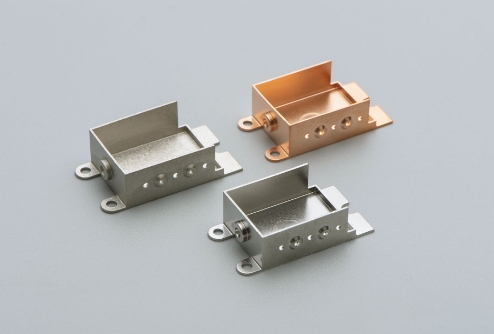
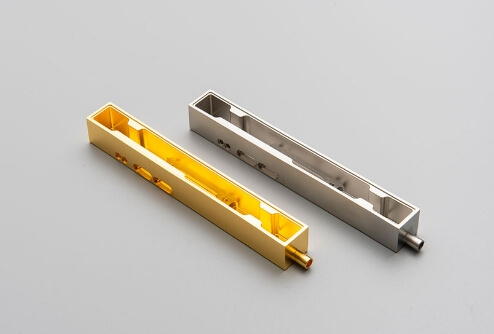
Quartz
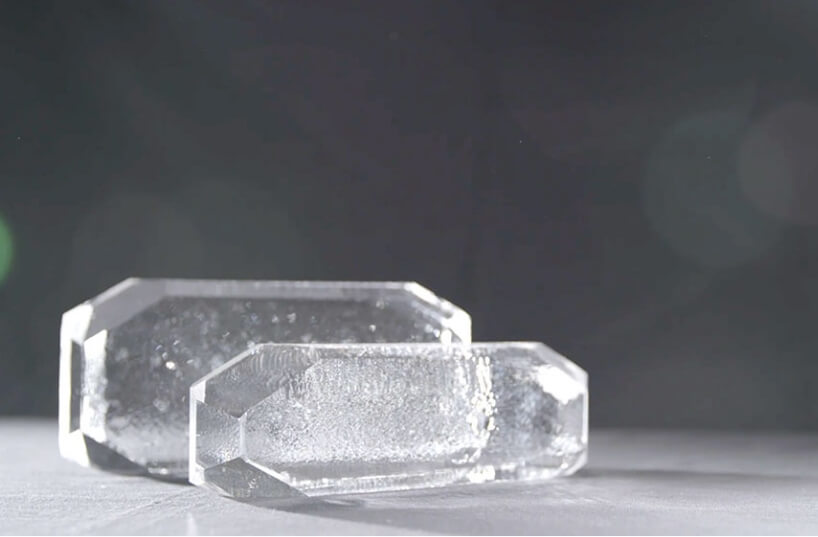
The world's largest breeding furnace and master craftsmanship that support the future of electronics
Synthetic quartz is utilized in quartz devices, which are key electronic parts that power essential electronic devices such as smartphones, PCs, TVs, digital cameras, watches, and automobiles.
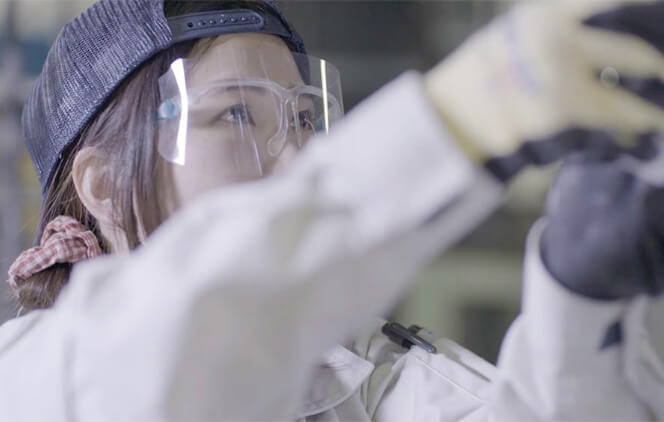
We manufacture synthetic quartz rough stones of world-class quality. These are used in the internationally renowned quartz devices of Seiko Epson Corporation, and are also widely used as a material for essential products around the world.
Please look at the following detailed sites.
Epson crystal device